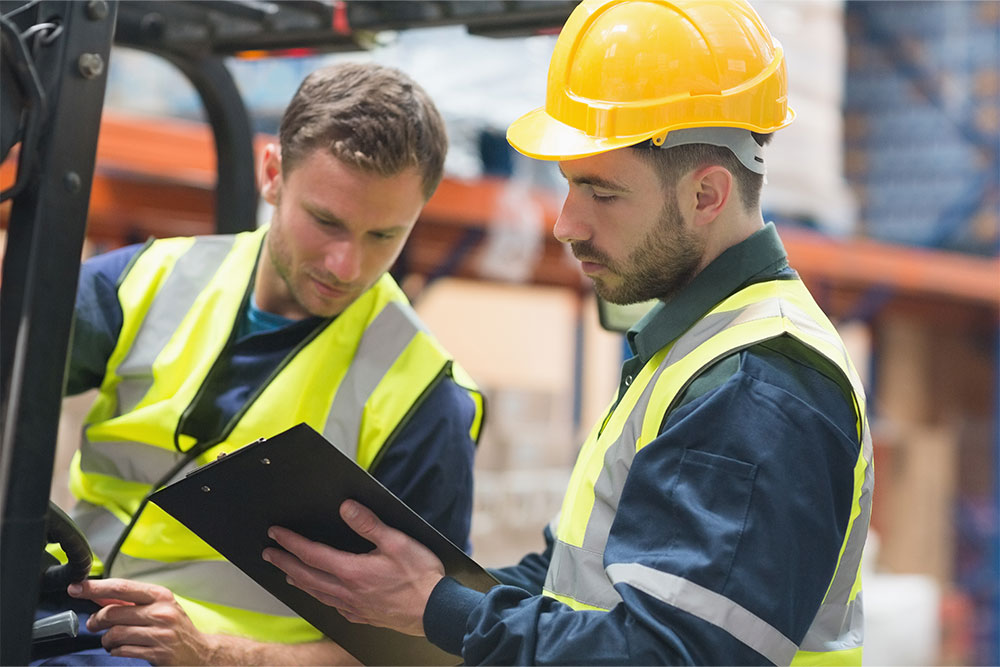
Warehouse safety can be hard to manage. A tour of the average one would probably feel like a live recreation of the Health and Safety Executive’s most discussed workplace hazards. And because these hazards are so commonplace, it’s easy to overlook them. Until an accident happens.
Our guide runs down the top five warehouse safety hazards and what you can do to control them. If you’re responsible for warehouse safety, refocusing on the big five can help you prevent accidents, reduce injury rates and save in the long term. Not to mention comply with health and safety legislation.
Warehouse Safety: Your Legal Duties
If you’re an employer, you have a legal duty to protect the health and safety of your staff and anyone else present in your workplace under the Health and Safety at Work etc Act 1974 (the HSWA).
The HSWA underpins all UK health and safety laws. It makes you accountable for any harm to employees (or members of the public) caused by your work activities.
To comply with the HSWA, you must follow the regulations and acts passed to support it – the most notable being the Management of Health and Safety at Work Regulations 1999. Under these regulations, you must carefully examine what might cause harm in your workplace and implement controls to prevent or reduce that harm. You probably recognise this process as risk assessment.
UK health and safety is risk-based, so the burden is on you to identify and manage risks before accidents happen. Our guide covers the leading causes of injuries in warehousing and storage. Recognising these often-overlooked hazards will help you carry out your risk assessment or review an existing one.
Accident Investigation
You can never reduce risks to zero. Accidents still happen even when workplaces are compliant with health and safety regulations. (Of course, they’re much more common and severe in non-compliant workplaces.)
Any accident should be thoroughly investigated to identify the root cause, not to find someone to blame. Revealing the underlying issue will let you fix it for good and prevent repeat incidents.
This approach is relevant to every workplace but is especially important for warehouse safety. The hazards listed below are sometimes thought of as part and parcel of warehouse work, and there’s nothing you can realistically do to manage them.
That’s not true. Although these warehouse safety hazards are widespread, they’re not unbeatable. If your workers are being harmed, it’s not the cost of doing business. There will be changes you can and must implement.
The 5 Biggest Warehouse Safety Hazards
The hazards discussed here are based on data from the Health and Safety Executive (HSE). This data can be found in the HSE’s Warehousing and Storage: A Guide to Health and Safety – HSG76.
This resource, which goes into more detail on these hazards and warehouse safety guidelines, can be found on the HSE’s website.
1. Slips and Trips
Slips or trips caused around a quarter (26%) of major injuries in warehousing and storage, more than any other incident type.
The fact that slips and trips cause so many major injuries suggests warehouse safety is often subpar for ordinary hazards. Since most workers wouldn’t consider losing their balance a significant risk, they rarely look out for slip and trip hazards. Of course, this attitude makes a painful fall more likely.
And a significant number of slips and trips are the result of human error. People either spill a liquid, creating a slipping hazard (called contamination by the HSE). Or they leave bulky items in the wrong place for someone to trip over.
These issues are made worse when workers either:
- Refuse to clean up after other people
- Don’t have the resources or know-how to tidy up properly
The first is a cultural issue. Make it clear that safety is always a shared responsibility and that everyone has a duty to correct or report hazards as soon as possible.
The second is a fault in your work systems. Designate areas for everything and give workers the tools and knowledge to tidy up contamination or properly stow tripping hazards.
2. Manual Handling
Manual handling was the second leading cause of injuries at 18% but the biggest contributor to absences over three days.
This inconsistency shows the difference between injuries and ill health. An injury is a one-off harmful incident. Ill health happens over a longer timeframe and is often tied to repeated events.
Unsafe manual handling is less likely to cause a significant injury. Instead, workers who regularly strain their bodies shifting objects tend to suffer from long-term back pain or musculoskeletal disorders (conditions that affect the bones, joints, tendons and muscles). Sufferers either live with chronic pain and the limits it puts on life or are forced to sign off work.
To protect your workers, eliminate as much manual handling as possible. You could mechanise or automate certain processes, for example, or arrange for goods to be delivered directly where they’re needed. If elimination isn’t a reasonable option, then all manual handling must be risk assessed and made as safe as possible.
We’ve written a lot about making manual handling safe. (Human Focus’ director, Ian Pemberton, started his career developing safer lifting techniques to protect warehouse workers.)
Some of the most important things to do are to train staff on the job and reinforce the learning periodically. Workers will get complacent or simply forget proper manual handling techniques unless they’re practical and practised regularly.
3. Work at Height
Coming in third is work at height, which accounted for 16% of major injuries.
Eliminating work at height is the safest solution, but like manual handling, elimination won’t always be possible. So, essential work at height must be risk assessed and made safe.
It’s critical you provide the safest possible platform for any work at height. For low-risk, short tasks, this is usually a ladder. (While the HSE doesn’t necessarily encourage ladder use, it’s definitely legal if done safely.)
A ladder won’t cut it if workers will be at height for a relatively long period (over 30 minutes) or are carrying out a complex task. Instead, consider using a mobile elevated work platform (MEWP) or even temporary scaffolding.
It should go without saying, but racking, forklifts, stacked pallets or other improvised ‘ladders’ are unacceptable. Competent workers know this, which is why you need to ensure that anyone working at height knows how to do it safely or is supervised by someone who knows how to do it safely.
Also, any ladders or other equipment should be checked before every use and subject to more detailed inspections at regular intervals. These duties come from the Provision and Use of Work Equipment 1998 (PUWER).
4. Being Hit by a Moving Object
Being hit by a moving object was responsible for 13% of major injuries.
The first step is to isolate areas where falling objects are a risk. Limit entrance to essential personnel and make sure it’s clearly marked.
You should also provide hard hats or other relevant personal protective equipment (PPE). But remember that PPE is considered the least effective control measure, as it only protects the worker. Consider all other options on the hierarchy of risk controls before resorting to PPE.
Some of the same control measures already mentioned can also help here. Objects that fall while being moved by mechanical means (pallet trucks or forklifts, for example) are a hazard. So, ensure that any vehicle operators are competent and able to manoeuvre around your warehouse space safely.
PUWER also applies to mechanical lifting equipment. You must inspect it regularly and fix any defects or faults that may cause the equipment to fail and endanger workers.
Extend similar checks to your pallets and racking. Never allow faulty equipment to be used, and organise replacements or repairs from a competent individual as soon as possible.
5. Being Hit by a Moving Vehicle
Being struck by a moving vehicle caused 10% of major injuries.
Many of these incidents happen when goods are loaded or unloaded since staff from other companies are involved, and staff from other companies may not be aware of your safe systems. So, ensure that you and your partners coordinate ahead of time. Share your risk assessments and communicate all relevant information to the parties involved in the exchange.
(Remember, you’re responsible for everyone’s health and safety when they’re on your site, even if they’re employed by someone else.)
For vehicles operating inside your warehouse, it’s essential to separate them from pedestrians as much as possible. Ideally, you’ll be able to provide separate routes for vehicles and pedestrians. If this isn’t possible, try to mark out separate tracks.
Reversing is another common hazard. Implementing a one-way system can avoid the need to reverse. Designating specific areas for reversing is less effective but still viable. Being able to manoeuvre vehicles safely is another reason all operators must be competent and licensed if necessary.
You also need to design procedures and safe work systems for:
- Coupling and uncoupling
- Ensuring load safety
- Preventing driveaways (moving a vehicle before the load is secure)
Warehouse Safety Training
These hazards are present in every warehouse environment, so you and your team need to be aware of them. They also need to know how to manage the risks they cause.
Our online Warehouse Safety Training course covers the hazards discussed in this blog, as well as fire safety – another universal concern in warehousing and storage. The course provides all workers with the essential warehouse safety tips they need to prevent accidents and protect their health. It also covers legal duties and incident reporting to encourage buy-in and get workers to flag and act on hazards consistently.