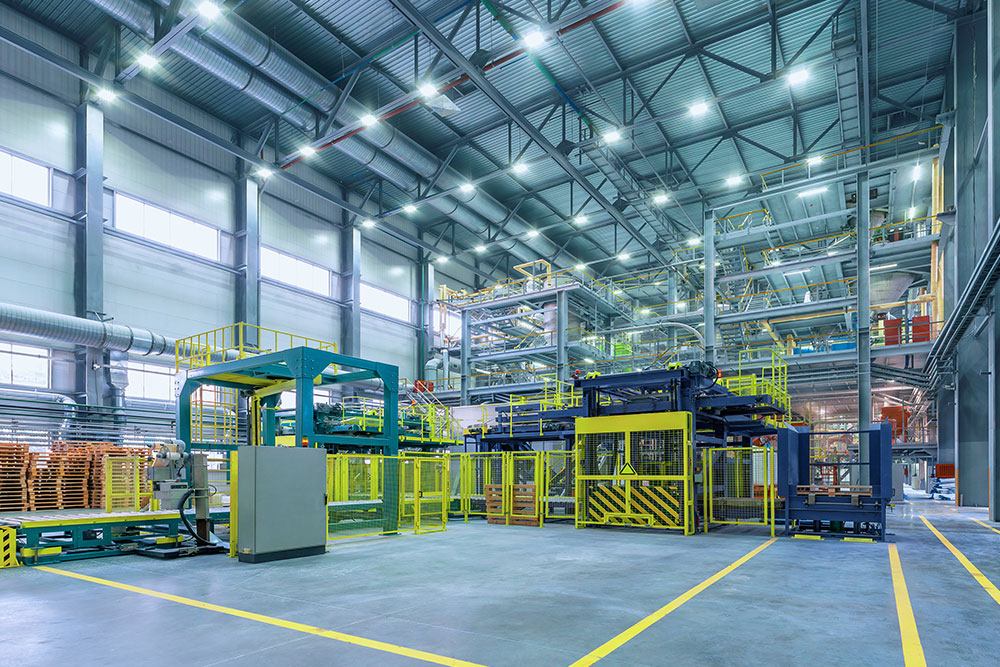
The Control of Major Accident Hazards (COMAH) Regulations are a crucial part of industrial safety in Great Britain. COMAH is designed to protect people and the environment by preventing major accidents involving dangerous substances, such as fuel, explosives and toxic chemicals. If your organisation handles, stores or produces such substances, you must comply with COMAH.
Key Takeaways
- COMAH Regulations aim to prevent and mitigate accidents involving dangerous substances, protecting people and the environment.
- COMAH applies to establishments handling dangerous substances, including chemical plants, fuel depots and food processing facilities.
- COMAH sites are categorised as high-tier or lower-tier, depending on the quantity and type of dangerous substances stored or processed.
- High-tier sites have stricter requirements, such as submitting safety reports and collaborating with local authorities on emergency plans.
Background
COMAH Regulations are Great Britain’s implementation of the European Union’s Seveso Directive. This directive was created in response to a catastrophic event on 10th July 1976 in the Lombardy region of Italy. The disaster involved the release of approximately 1kg of 2,3,7,8-tetrachlorodibenzo-p-dioxin (TCDD), a highly toxic chemical.
The impact was severe:
- Over 3,300 animals died immediately, and an additional 80,000 were slaughtered to prevent contamination of the food chain.
- Approximately 200 people developed chloracne, a serious skin condition caused by dioxin exposure.
This tragedy served as a wake-up call and led to the development of strict regulations to prevent similar incidents. The EU introduced these as the Seveso Directive, which was first incorporated into British law as the Control of Industrial Major Accident Hazard (CIMAH) Regulations in 1984.
In 1997, the Seveso Directive went through a major overhaul, becoming the Seveso II Directive. Great Britain updated its own version accordingly, and CIMAH became COMAH – the Control of Major Accident Hazard Regulations. These regulations were updated in 2015 (COMAH 2015) to reflect advancements in safety practices and align with changes in the European Union’s Seveso III Directive.
Past Incidents in Great Britain
- Buncefield Oil Depot Explosion (2005): One of the most notable COMAH-related incidents in Great Britain, the Buncefield explosion occurred at a fuel storage depot in Hertfordshire. It was caused by the overflow of petrol during a transfer operation, leading to a massive vapour cloud explosion. The accident caused extensive damage to nearby properties and injured over 40 people.
- Flixborough Disaster (1974): The Flixborough disaster involved an explosion at a chemical plant in Lincolnshire caused by a cyclohexane vapour cloud. The explosion killed 28 people and injured 36 others.
Key Components of COMAH Regulations
Dangerous Substances
COMAH Regulations apply to sites that store, handle, or process specified quantities of dangerous substances capable of causing significant harm to people or the environment during a major accident. Sites where dangerous substances are produced as a byproduct must also comply with COMAH if the quantities exceed the specified thresholds.
The most notable dangerous substances are:
- Explosives: Chemicals with the potential to cause explosions, such as ammonium nitrate and fireworks.
- Flammable Liquids and Gases: Substances that can ignite easily, such as liquefied petroleum gas (LPG), petrol and ethanol.
- Toxic Substances: Chemicals hazardous to human health, including chlorine, ammonia and hydrogen sulfide.
- Environmental Pollutants: Materials that pose a risk to the environment, such as persistent organic pollutants (POPs) or heavy metals like mercury.
Applicability
COMAH Regulations apply to a diverse range of industries that store or handle dangerous substances, including:
- Chemical manufacturing and storage sites (comprising 25% of all COMAH establishments in Great Britain)
- Oil refineries and petrochemical plants
- Explosives and fireworks manufacturing and storage sites
- Fuel storage depots
- Food processing plants
- Warehouses and distribution centres
- Mining and quarrying operations
- Water treatment works
The Competent Authority
COMAH compliance is enforced by the competent authority – a partnership between the Health and Safety Executive (HSE) and the relevant environmental regulator. This regulator is the Environment Agency in England, the Scottish Environment Protection Agency in Scotland or the Natural Resources Wales in Wales.
Together, they oversee safety and environmental standards through inspections, safety report reviews, and incident investigations. However, not all COMAH sites are subject to the same level of oversight.
High-Tier vs. Lower-Tier Sites:
Under COMAH, sites are categorised into two tiers based on the type and quantity of dangerous substances stored or processed.
High-Tier Sites:
- Exceed the higher threshold quantities of dangerous substances as specified in COMAH.
- Subject to more stringent regulatory requirements, including submitting detailed safety reports to the competent authority.
- Must prepare both on-site emergency plans and work with local authorities on off-site emergency plans.
- Require regular inspections and audits by regulatory authorities to ensure compliance.
Lower-Tier Sites:
- Contain hazardous substances between the upper and lower threshold.
- Have fewer regulatory requirements but must still implement robust risk management measures.
- Required to notify the competent authority about the nature and quantity of hazardous substances on site.
- Must conduct periodic reviews of safety practices to prevent major accidents.
According to the UK Government, there are approximately 950 COMAH sites in Great Britain, classified as either upper-tier or lower-tier.
Threshold Quantities
COMAH Regulations apply when the quantity of dangerous substances stored or handled at a facility meets or exceeds the specified threshold limits detailed in the legislation. These thresholds are defined for each substance and vary depending on their classification under the CLP (Classification, Labelling and Packaging) Regulations.
Examples of threshold quantities for some common substances include:
- Ammonium nitrate: 2,500 tonnes (Lower-tier) and 5,000 tonnes (Upper-tier).
- Chlorine gas: 10 tonnes (Lower-tier) and 25 tonnes (Upper-tier).
- Petrol: 2,500 tonnes (Lower-tier) and 50,000 tonnes (Upper-tier).
The thresholds are designed to ensure a proportionate response, with higher quantities requiring additional safety measures.
Risk Assessment
Hazard Identification: Operators (individuals or organisations with control over the site) must systematically identify potential risks associated with dangerous substances on-site. This includes:
- Assessing chemical properties (flammability, explosiveness, toxicity).
- Evaluating storage conditions, including pressure, temperature and containment systems.
- Identifying failure scenarios such as leaks, fires, explosions or equipment malfunctions.
Preventative Measures: Operators must implement and regularly review preventative controls to reduce the likelihood and impact of major accidents. These measures may include:
- Regular maintenance of equipment and safety systems.
- Installation of automated monitoring and alarm systems for early detection of leaks or failures.
- Staff training on safety procedures and hazard awareness.
- Ensuring appropriate storage and segregation of incompatible substances to prevent hazardous reactions.
Safety Reports (High-Tier Sites): High-tier sites are legally required to submit safety reports to the competent authority. These reports must include:
- Detailed risk assessment findings.
- Preventative measures such as fire suppression systems, leak detection and secondary containment.
- Emergency plans, including evacuation procedures, communication strategies and coordination with local emergency services.
Emergency Planning
Internal Emergency Plans: All COMAH sites must prepare and maintain internal emergency plans to respond effectively to potential accidents. These plans should:
- Outline immediate actions to contain and control accidents, such as isolating leaks or extinguishing fires.
- Define roles and responsibilities for staff during an emergency.
- Include procedures for alerting and evacuating workers and other on-site personnel.
- Incorporate provisions for first aid, spill containment and decontamination.
External Emergency Plans (High-Tier Sites): High-tier sites are required to collaborate with local authorities to develop external emergency plans. These plans ensure a coordinated response involving multiple stakeholders, including:
- Emergency services (fire, police, ambulance)
- Local authorities and environmental agencies
- Nearby businesses and the surrounding community
The plans must detail evacuation routes, public communication protocols and resources available for large-scale incident management.
Collaboration and Communication: Effective emergency preparedness relies on strong collaboration between operators, local authorities and emergency services. This includes:
- Regular training exercises to test emergency plans and identify gaps.
- Public communication strategies to inform nearby communities about potential risks and appropriate actions during an incident.
- Sharing information with emergency services about on-site hazards and response strategies.
Legal Responsibilities Under COMAH
Operators of COMAH sites have several legal duties, including:
- Safe storage and handling of hazardous substances.
- Submission of detailed safety reports for high-tier sites.
- Development and maintenance of emergency plans to manage potential incidents.
- Cooperation with the competent authority during inspections.
Non-compliance can result in significant penalties, including fines, legal action and reputational damage.
COMAH Training
Training is crucial for ensuring compliance with COMAH Regulations. It helps workers at COMAH sites understand their roles in identifying, controlling and managing major accident hazards.
Our IIRSM-approved online COMAH training course outlines the responsibilities of employees under COMAH. Workers will understand their duties to identify and manage major hazards, report incidents and follow established safety management protocols. This awareness is vital for maintaining compliance and preventing serious accidents.
Upon completing the course, workers will be better equipped to implement control measures, identify weaknesses in safety systems and fulfil COMAH requirements effectively.