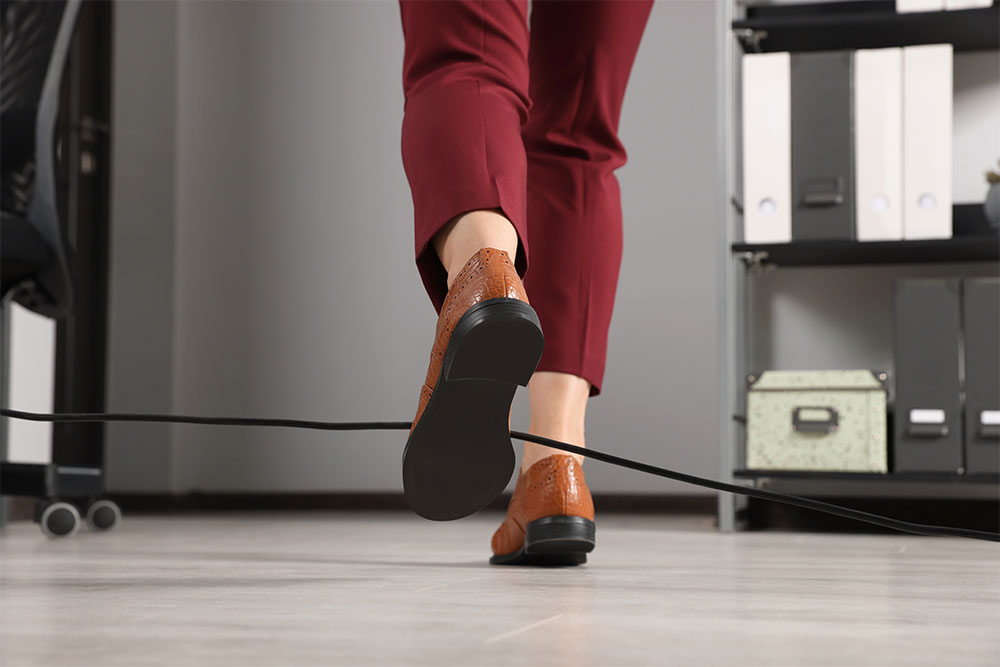
A near miss incident is any event where someone might have been hurt, but no actual injuries occurred. You’ve probably experienced one of these close calls. You might have lost your footing on a slippery floor before catching yourself. Or dropped a kitchen knife millimetres from your toe.
Luck is the only reason a near miss doesn’t become an accident. But being lucky is not an acceptable solution for workplace safety.
This guide explains what near miss incidents are, why they matter and how you should handle them at work. Because recording near misses and acting on the information you gather is a vital safety management strategy.
What is a Near Miss Incident?
A near miss is any hazardous situation, event or act that could have resulted in injury but didn’t.
The only difference between a near miss and an accident is the outcome. In an accident, someone is actually harmed, whereas everyone walks away unscathed in a near miss.
While near misses are less severe than accidents, both are cause for concern. And both are treated largely the same way by experienced safety managers who recognise that near misses and accidents share root causes.
So, by investigating near misses as thoroughly as you would an accident, you can find and fix underlying issues before someone’s actually hurt.
What is an Adverse Event?
An adverse event is any unwanted situation or occurrence. This term describes both near misses and accidents because they share the same DNA. Both are an unwanted consequence of some shortcoming in your safety arrangements.
Examples of Near Miss Incidents
A near miss incident is any scenario that has the potential to cause harm. Sometimes, they’ll be a full-on catastrophe, where someone’s life is spared by the narrowest of margins.
For example, a crane might fail on a construction site, dropping a steel beam to the ground below. But because a worker decided to stop a moment and check his phone, he wasn’t standing where the steel beam hit.
Others are less dramatic. Workers might take risky shortcuts, such as climbing on boxes to reach a high shelf because it’s faster than using the supplied ladder. Or they might cut across a wet floor because they don’t have time for a detour.
In fact, these scenarios might not even register as near misses to the workers involved. But on another day, these bad decisions might just end in a trip to the hospital.
What do Near Misses Mean?
Near misses are dress rehearsals for potential accidents. They involve all the same conditions, factors and players, but some element of luck means no one gets hurt.
This overlap is why competent safety managers see near misses as a gift. Studying them will reveal issues that have the potential to cause harm but haven’t yet.
But not everyone sees near misses this way. We remember painful situations much more easily than mundane ones because of the way our brains work. (Dropping a knife on your toe is a lot more memorable than dropping one near it.) As a consequence, we consider near misses less important than accidents.
Workers who experience a close call often carry on as if nothing’s happened after a quick sigh of relief. Similarly, if a shortcut doesn’t result in any negative consequences, it’s easy for workers to assume it wasn’t risky and can be repeated.
But near misses mean there’s either a problem with your safety arrangements or something or someone has failed. You should take the opportunity to find and fix the issue before it causes a painful accident.
Is it Necessary to Report Near Misses?
It’s always beneficial to report near misses. Handling them the same way you would an accident will help improve workplace safety.
Certain near misses must also be reported to the Health and Safety Executive (HSE) under the Reporting of Injuries, Diseases and Dangerous Occurrences Regulations (RIDDOR).
You can find the complete list of these ‘dangerous occurrences’ on the HSE website. But some to be aware of are:
- Explosions or fires that cause a minimum 24-hour work delay
- Release of flammable gases that would cause a fire/explosion if ignited
- Release of substances hazardous to health, such as asbestos or diisocyanates
The HSE should be notified of these dangerous occurrences for the same reason near misses should be reported at work: it helps prevent future accidents.
Learning what went wrong and how it can be avoided will make your workplace safer and often more productive.
Why is it Important to Investigate Near Miss Incidents?
If you don’t investigate near miss incidents, they’re liable to happen again. And when they do, the consequences are likely to be more severe. You can only be lucky so many times, as shown by the accident triangle.
The accident triangle (also known as the safety triangle) represents the relationship between major accidents, minor accidents and near misses. It was originated by Herbert Heinrich (hence the initial name Heinrich’s triangle) and later refined by Frank Bird (Bird’s triangle is yet another alternative name).
Bird’s research suggested that for every serious accident, there were 600 near misses (plus 10 minor accidents and 30 accidents causing property damage).
Although these figures have since been disputed, it’s agreed that near misses far outweigh accidents. That means you potentially have hundreds of opportunities to investigate and correct safety issues before anyone’s seriously injured. But only if you handle near misses correctly.
What is a Near Miss Incident? – Key Takeaways
- A near miss is any situation, event or act that could have caused harm but didn’t.
- Near misses are a warning sign that something in your safety arrangements needs attention.
- Investigating near misses helps you find and fix safety issues before they cause accidents.
Learning How to Investigate Near Misses
Investigating near miss incidents is key to preventing accidents and creating a safer work environment.
Our online Near Miss Training covers recognising, reporting and investigating near misses effectively. It explains how to work with employees to capture near miss reports and analyse the underlying issues that caused the adverse event. This proactive approach gives you the insights you need to make meaningful improvements to work systems that prevent accidents and improve productivity.