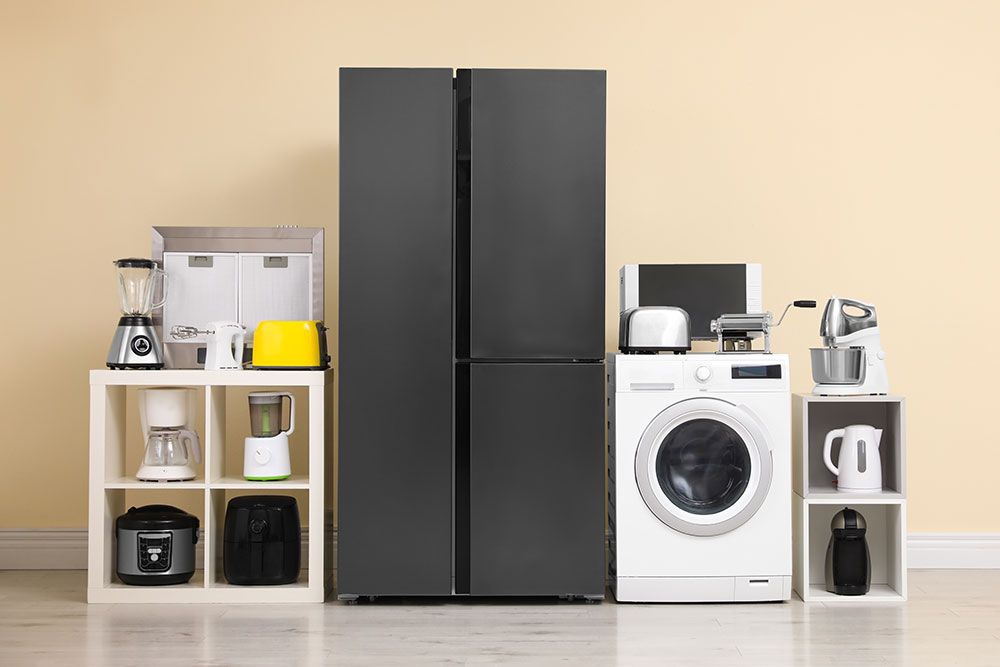
White goods aren’t typically seen as a fire risk. But you’re obviously more clued up than most people because you know appliances do cause fires. So, which white goods can be a fire risk?
This guide explains which appliances to watch. It will help employers and property owners meet their fire safety duties and handle fire risks from all appliances, big and small.
Understanding Fire Risk in White Goods
We expect kitchen appliances at work. Kettles and fridges are probably equally as important for productivity as computers and phones in British workplaces. Not to mention the daily dishwasher cycle.
These appliances make our work (and home) lives easier but can also be fire hazards if not managed properly.
Electrical faults, poor maintenance and improper use are common issues that can lead to fires. These hazards are often worse in the workplace because employees pay little attention to white goods as long as they work.
While workers should check appliances regularly, employers are responsible for white goods fire safety. All electrical appliances present an inherent fire risk and must be managed accordingly under fire safety regulations.
What Fire Safety Regulations Say
Under the Regulatory Reform (Fire Safety) Order 2005 (FSO), the “responsible person” in any non-domestic premises must ensure fire safety. This role falls to the employer in workplaces or building owner or manager for other non-domestic properties
The most important duty under the FSO is conducting a fire risk assessment. This assessment starts with identifying hazards that may start a fire. Faulty wiring or malfunctioning electrical appliances are some of the most common ignition sources to look out for.
By regularly checking and maintaining your appliances, you can significantly reduce fire risks.
Common White Goods That Pose a Fire Risk
Which white goods can be a fire risk? Any appliance can start an electrical fire, but several white goods present additional fire risks.
Washing Machines
Washing machines are essential in some workplaces but can be dangerous if not maintained. Overheating, electrical faults and mechanical issues can lead to fires. Regularly check for signs of wear and tear and ensure the machine is serviced as recommended by the manufacturer.
Tumble Dryers
Tumble dryers are notorious for fire risks due to flammable lint build-up in filters and vents. Fortunately, tumble dryers are rare in workplaces. If you do have one, it’s important to clean the lint filter according to the manufacturer’s recommendations.
Refrigerators and Freezers
Refrigerators and freezers run continuously, so they pose fire risks around the clock. Improbably, they’re also prone to overheating. Keep enough space around your fridge or freezer to allow airflow, and regularly check the appliance’s vents for blockages.
Refrigerants (the chemicals that keep fridges cold) can also be flammable. Be vigilant for any leaks, particularly when moving a fridge or freezer. And never use a sharp tool to clear ice from the inside walls.
Dishwashers
Water and electricity famously don’t mix well. Regularly check hoses and connections for leaks and ensure the appliance is properly maintained and serviced.
Ovens and Microwaves
Both ovens and microwaves can overheat, especially if they’re old or rarely cleaned. Grease, oil and crumbs are also flammable so potential fuel sources. Allowing food debris to build up in an appliance that generates extreme heat is an obvious fire risk.
Best Practices for White Goods Fire Safety
Preventing electrical fires in the workplace involves more than just knowing which white goods can be a fire risk.
Implementing best practices and consistent safety measures can help you manage these risks effectively. Here’s how you can enhance white goods fire safety:
Investigate Faults
Investigate any appliance, new or old, that shows signs of deterioration, such as frayed cords, unusual noises or spotty performance. Don’t ignore these warning signs.
Have the appliance in question checked by a qualified engineer. Addressing minor issues promptly can prevent major problems and potential fire hazards.
Invest in New Appliances
Newer typically means safer white goods. Appliances designed and built under modern manufacturing standards should present fewer risks. So, if suitable, replace older models with newer ones.
Check Second-Hand Appliances
Second-hand appliances are still a safe (and economical) option if they’re properly checked. Ensure that any used white goods have been inspected by a competent person and deemed electrically safe.
Carry Out Maintenance and Inspections
Schedule regular maintenance for all white goods. Arrange for a competent person to check for signs of wear and tear and carry out maintenance as needed.
You should also arrange for regular portable appliance testing (PAT). Despite the name, PAT can determine whether stationary electrical appliances (such as bulky white goods) are electrically safe.
Finally, maintenance should include cleaning. All vents should be cleared regularly, and any build-up of dirt or grease inside an appliance should also be dealt with.
Position White Goods Safely
White goods are heavy and difficult to move, so consider carefully where you position them.
As mentioned, some white goods overheat if there’s no space around the appliance for airflow. You must also keep flammable materials a safe distance from any appliances that generate heat (ovens, microwaves and toasters, for example).
White goods can also obstruct doorways or corridors. All escape routes must be clear in a fire emergency, so carefully consider where your white goods are placed.
General Fire Safety Advice
While we’ve focused on white goods fire safety, the principles apply to all electrical equipment in the workplace. They also crossover with more general fire safety duties.
Electrical Safety
Like white goods, other electrical equipment can pose fire hazards if not properly maintained. Consistently check all electrical devices for signs of wear and tear, such as frayed cords or overheating.
It’s also considered best practice to regularly put electrical appliances through a PAT test. Ensure that any faulty equipment is repaired or replaced promptly. Any repaired appliances should be tested again before being put back into service.
Using surge protectors and avoiding overloading sockets can further prevent electrical fires.
Preparing for Emergencies
Planning for fire emergencies is essential for maintaining a safe workplace. Here are some steps to ensure you’re prepared:
- Conduct Regular Fire Drills: Fire drills help employees know what to do in an emergency. Practice evacuations regularly to ensure everyone can leave the building quickly and safely.
- Maintain Clear Evacuation Routes: Ensure all exits and pathways are unobstructed. Clearly mark evacuation routes and keep them free from any obstacles.
- Equip Your Workplace with Fire Safety Equipment: Install smoke detectors, fire alarms and fire extinguishers per your fire risk assessment. Make sure all firefighting equipment is regularly maintained and in working order.
- Develop an Emergency Plan: Create a detailed fire emergency plan outlining the steps to take in case of a fire. Ensure all employees are familiar with the plan.
Staff Training and Awareness
Educating your employees about fire safety is crucial. Provide training on fire prevention, how to safely handle firefighting equipment and what to do in case of a fire.
Employees should be aware of electrical fire risks and know how to spot potentially hazardous appliances.
Which White Goods Can Be a Fire Risk – Key Takeaways
- Employers are responsible for fire safety in the workplace. Part of this duty is ensuring electrical appliances are safe.
- Employees should regularly check white goods for signs of electrical faults, such as frayed cords or unusual noises, and ensure they are kept clean to prevent fire risks.
- Any fault is a warning sign. Strange noises, overheating or spotty performance indicate possible issues. Take questionable appliances out of service until checked and repaired by a professional.
- Conduct thorough fire risk assessments. Malfunctioning electrical appliances are a potential ignition source and must be managed accordingly.
Fire Risk Assessment Training
Ensuring the fire safety of white goods and other electrical appliances is just one of the responsible person’s duties. To fully equip yourself with the skills needed to manage fire risks, consider enrolling in our online Fire Risk Assessment Training.
Fire Risk Assessment Training teaches how to identify fire hazards and the measures to eliminate or control them. It ensures that you’re well-prepared to handle fire safety duties and demonstrates a commitment to maintaining a safe workplace, complying with the Fire Safety Order and protecting property and lives.