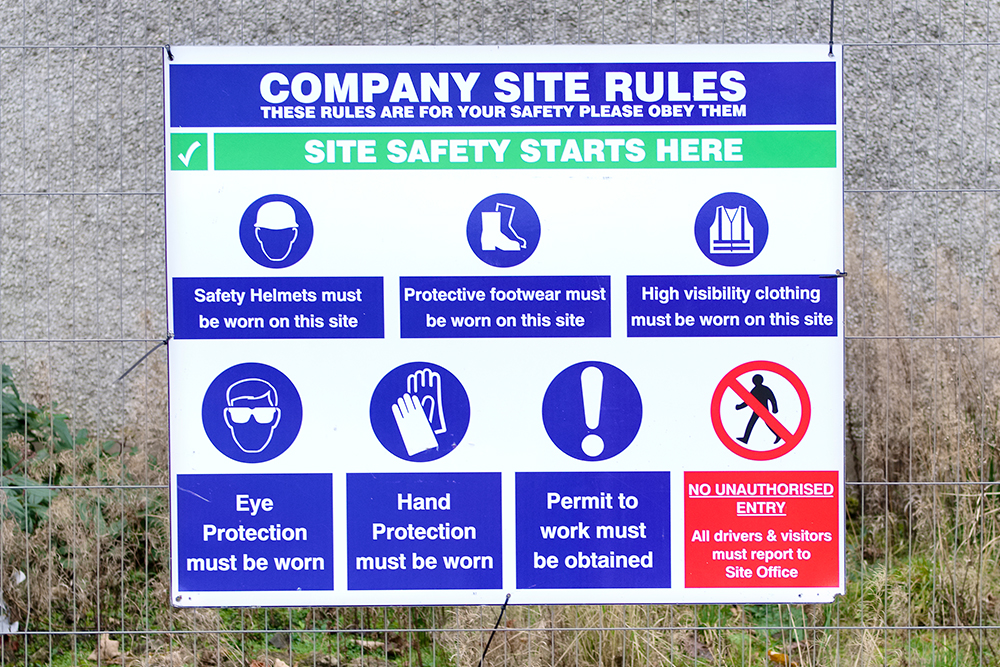
PPE signs are necessary if personal protective equipment (PPE) is used in your workplace. These signs act as reminders, keeping PPE at the forefront of your workers’ minds and making it more likely they’ll use it as instructed.
This guide explains what to consider when implementing mandatory PPE signs. It also covers safety sign regulations and practical advice on keeping them noticeable and relevant to your workers.
Personal Protective Equipment Explained
Personal protective equipment refers to any equipment or clothing used by a worker to protect against risks to their health and safety. Examples include hard hats and safety goggles to fall arrest restraints for workers at height.
There are limiting factors when it comes to PPE effectiveness. Firstly, as the name makes clear, it’s personal protection. PPE only makes the individual using it safer and does nothing to reduce broader risk levels. This narrow application makes PPE the least effective risk control. PPE is a worker’s last line of defence after all other safety measures have been implemented or ruled out.
Secondly, PPE is only beneficial when deployed properly, which depends on the user’s understanding of the equipment and willingness to wear it. It’s this potential for worker complacency that makes PPE signage necessary.
Safety Sign Legislation
The need for PPE signs isn’t explicit in UK health and safety law. Still, they are typically necessary to meet employer duties established in two regulations.
The first is the Health and Safety (Safety Signs and Signals) Regulations 1996, which govern general safety sign use. These regulations state:
So safety signs must be used if they’ll make people safer. PPE signs fit this description. Protective gear is often overlooked by inexperienced or apathetic workers, particularly in workplaces where a strong safety record has allowed complacency to creep in. In these situations, well-placed PPE signage at the entrance of a hazardous area could be the difference between a worker wearing their protective gear or not.
PPE Sign Legislation
PPE use is legislated by the Personal Protective Equipment at Work Regulations 1992 (PPER). Under these regulations, employers must provide suitable PPE to all employees if it’s necessary for their protection. This is the second set of regulations that essentially make PPE signage necessary, with two standing out in particular:
- Regulation 9 requires employers to give workers adequate information, instruction and training on the proper use of any issued PPE
- Regulation 10 requires employers to take all reasonable steps to ensure that issued PPE is properly used
The Health and Safety Executive’s guidance on PPE makes it clear how PPE signs support compliance with these regulations:
The PPE signs referenced by the Health and Safety Executive (HSE) here are mandatory.
Mandatory Signs
Mandatory signs are reminders of what must be done to stay safe and compliant when in a particular area of a workplace. They’re one of the primary types of PPE signs, with every example offered by the HSE’s safety sign guidance related to the use of protective equipment. All share similar intrinsic features: round shape with a white pictogram over a blue background.
These signs will remind and encourage employees to use PPE when necessary.
Warning Signs
It may sometimes be necessary to use warning signs, too. These safety signs warn workers of a particular hazard in an area – asbestos, for example. Combining that information with a mandatory sign reminding workers to use the corresponding PPE (protective clothing in this example) may have more of an impact. It’s a known fact that explaining why safety measures are necessary helps workers comply.
How to Place PPE Signs
The HSE states that PPE signs should be placed at entry points of hazardous areas where protective equipment is necessary. Signs must be noticeable, so position them somewhere that can’t be missed.
Signs should also be clear and easy to understand, which is why safety signs all share recognisable intrinsic features. Ensure any PPE signs are sufficiently large and readable regardless of the time of day or lighting conditions.
But limit how many signs are close to each other. Overlapping instructions makes workers likely to miss critical information or misunderstand necessary details.
Similarly, only keep signs up for as long as they’re relevant. If a PPE sign is enforcing the use of obsolete equipment, workers might assume the same of other signs. This misconception might lead them to question or ignore safety instructions in different areas.
How to Avoid Sign Fatigue
Of course, workers can still become blind to relevant signs. This issue – known as sign fatigue – is common. Workers exposed to a sign every day eventually stop paying attention, leaving critical PPE signage as nothing more than wallpaper. Periodically changing the placement, design, or sign is essential to keep messages noticeable. However, any changes must still retain the standard intrinsic features outlined by HSE.
People like novelty, and even a bright, new version of the same old sign will likely recapture workers’ attention. You can achieve a similar effect by cleaning and rehanging an old sign, making it seem fresh again.
And regular upkeep or replacement shows your workers you care about the signs. Like any safety initiative, using PPE signage will be more successful if the higher-ups are clearly invested.
PPE Training
PPE signs are one part of compliance with PPER. But it’s pointless to remind your workers about PPE if they don’t know how to use it, so appropriate training is also mandatory.
Our online PPE Training course offers instructions on using, caring for and storing the most widespread and versatile protective equipment. It gives PPE users the understanding they need to deploy protective gear successfully. At the same time, employers can prove they’ve provided relevant training. Users also learn practical maintenance and hygiene tips, helping them keep their PPE compliant and working.