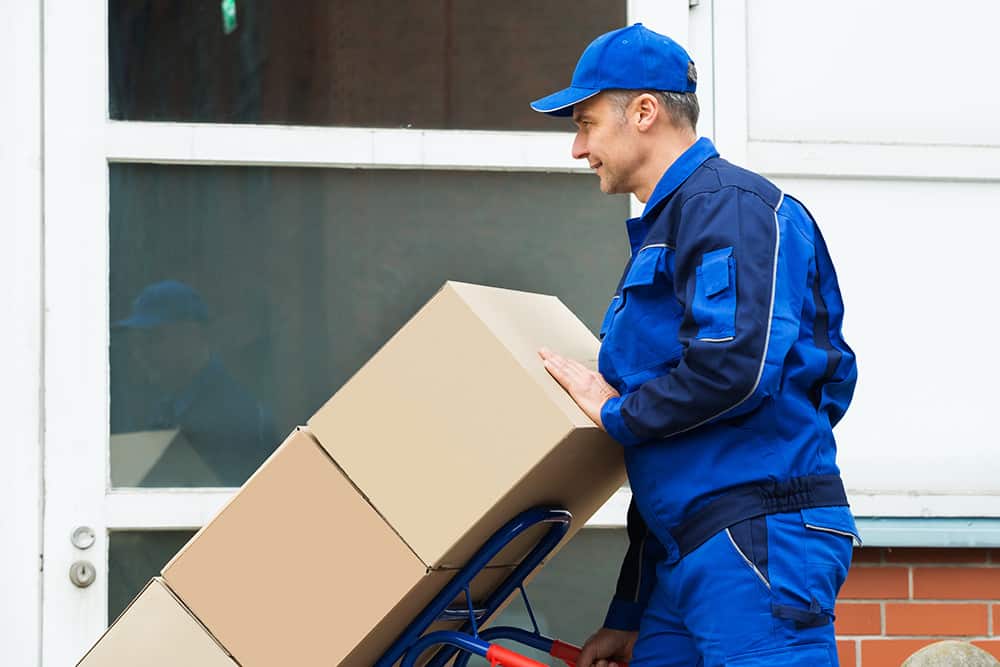
Under UK health and safety legislation, employers are obligated to protect their employees’ health, safety and welfare. One of the primary causes of workplace injuries is the lifting and moving of loads, also known as manual handling.
To help prevent these injuries, you should apply the hierarchy of manual handling. It’s a simple framework that outlines the most effective control measures in the order they should be implemented.
Understanding the hierarchy and applying it consistently will help prevent manual handling injuries and prove that steps have been taken to protect workers.
The Risks of Incorrect Manual Handling Techniques
According to the Health and Safety Executive (HSE), more than 500,000 workers suffered from a work-related musculoskeletal disorder (MSD) in the most recent reporting year.
MSDs are defined as conditions and injuries that cause pain to the back, joints and limbs. A significant number of these injuries were caused by incorrect manual handling at work.
Manual handling encompasses activities that involve lifting, pushing, pulling, lowering and carrying loads using physical force. If not performed correctly, any of these activities can result in either a short-term or long-term manual handling injury.
Some of the risks of improper manual handling techniques include:
- Back injuries
- Sprains and strains
- Hand injuries
- Leg injuries
- Slip, trip and fall injuries
- Hernias
- Foot injuries
- Cuts and bruises
- Joint and muscle pain
- Broken bones
- Inflammation
- Repetitive strain injury (RSI)
Legislation, including the Health and Safety at Work Act 1974 and the Manual Handling Operations Regulations 1992, places a legal obligation on employers to eliminate or at least reduce the risks of manual handling accidents and injuries.
A failure to comply can result in significant fines and claims against your organisation.
What Is the Manual Handling Hierarchy of Controls?
Whenever work activities pose a threat to health and safety, employers must carry out an appropriate risk assessment.
This duty extends to hazardous manual handling. You need to carefully examine the task, environment, and workers to identify hazards and determine the likelihood and severity of an injury (the risk).
Once you know the risks, you need to take appropriate steps to manage them. This is where you should apply the manual handling hierarchy of controls.
When used in conjunction with correct techniques, he manual handling hierarchy of controls will help you eliminate or reduce risks to a “reasonably practicable” level, as required by law. It helps employees take a consistent and safe approach when performing manual handling tasks.
What Are the Five Hierarchies of Control for Manual Handling?
There are five levels in the manual handling hierarchy of controls. Each level is designed to eliminate or mitigate manual handling risks.
You should always begin with the most effective control – eliminating the need to manually handle the load altogether. If elimination isn’t practical, you move down the hierarchy, selecting the next most effective and feasible control. The goal is to apply the highest level of control reasonably practicable in your specific work environment.
The five hierarchies of control for manual handling are:
- Elimination – Removing the risk entirely by avoiding the need for manual handling.
- Substitution – Decreasing the overall weight of the load by splitting it into smaller sections, or by using multiple employees to move the load.
- Engineering controls – Using different work practices, lifting equipment or mechanical aids to reduce the risk of manual handling injury.
- Administrative controls – Changing work practices to ensure that employees are not overworked. Administrative controls also include providing proper moving and handling training.
- Personal protective equipment (PPE) – Providing employees with PPE that can reduce the risks of manual handling. This can include reinforced non-slip footwear or gloves.
A combination of controls is often necessary to comply with health and safety legislation and effectively manage manual handling risks. Relying on a single control measure may not be sufficient, especially in complex or high-risk tasks.
What Are the Five Steps of Manual Handling?
Every workplace is different and requires employees to perform a variety of manual handling tasks. This diversity makes it challenging to establish precise rules that perfectly fit every manual handling situation. However, following basic procedures can help reduce the risk of a manual handling injury occurring.
Health and safety experts have developed five key steps that can be followed to ensure safe manual handling at work. Often referred to as the “five Ps”, these steps can greatly reduce the likelihood of manual handling accidents.
If a manual handling task cannot be avoided altogether, the five steps to follow are:
- Step One: Plan – Assess the environment and the load to be moved. Make sure the way is clear and that the floor is not slippery. Decide if one person can move the object or if two or more may be needed.
- Step Two: Position – Make sure your body is in the correct position to move the load. Centre your body and feet. Place your feet apart with one leg slightly forward. Bend at the knees and not with your back. Make sure you have a firm grip on the object.
- Step three: Pick – When lifting, use your leg muscles to generate momentum, not your back muscles. Keep the object close to your body and lift it with a fluid, natural motion.
- Step Four: Proceed – When carrying the load, hold it close to your body and keep your spine, head, and neck straight. Do not twist, bend, or reach when carrying a load.
- Step Five: Place – When lowering the load, maintain good posture and bend at the knees, not the back. Move slowly and avoid dropping the load.
What Must You Consider When Manual Handling?
- What are your capabilities to lift? Consider your own height and strength.
- What limitations do you have? Consider any existing health conditions that may be worsened by the activity. Never conduct any manual handling unless you’re confident it won’t put you at an unreasonable risk of injury.
- How heavy is the load? Should it be split? Generally, any load that weighs 20 kilograms or more should be split, and the parts lifted individually. However, you may need to reduce this limit where conditions dictate – for example, when the loads are particularly unstable or difficult to grip.
- Is it easy to grip the load? Loads larger than 75 centimetres in any direction may be difficult to hold.
- Is one side of the load heavier than the other? The heavier sides of loads should be held closer to the chest.
- Is the load stable? If the load is unstable, it may be unsafe.
- Are there space constraints that require you to use unnatural postures?
- Are floors slippery, uneven, or cluttered?
- Are there variations in floor levels?
- Is there enough lighting?
- Is the temperature suitable? Extremely hot or cold temperatures can increase the risk of injury from manual handling tasks.
When Should the Hierarchy of Manual Handling Be Applied?
The hierarchy of manual handling should be used routinely as part of the planning and assessment of manual tasks.
Use the hierarchy in the following situations:
- Before starting a new task – Any task that involves lifting, pushing, pulling, or carrying should be assessed in advance using the hierarchy.
- When planning or reviewing workstations or processes – If the layout or equipment used in a job changes, revisit the hierarchy to ensure risks remain controlled.
- After incidents or near misses – If an injury or close call occurs, reassess the task using the hierarchy to identify missed or failed controls.
- During routine risk assessments – Periodic health and safety risk assessments should include the hierarchy of manual handling controls to identify improvements.
- When loads or materials change – If a load becomes heavier, more awkward, or needs to be moved more often, controls should be reconsidered.
Applying the hierarchy early ensures risks are controlled appropriately. It helps employers meet legal duties and prevents poor handling from becoming normal practice.
Create a Safer Workplace with Training
As an employer, you must provide a safe workplace for your employees. If their tasks involve moving heavy loads, then providing moving and handling training is a legal obligation. Failure to do so can result in workplace injuries or accidents as well as penalties from regulators.
Reduce risks at work and invest in online manual handling courses from Human Focus. The courses will help you and your team carry out your duties safely and in line with legislation.
Human Focus covers all aspects of manual handling for a range of sectors. Whether you work in an office or a warehouse, it’s essential to learn how to move loads safely.