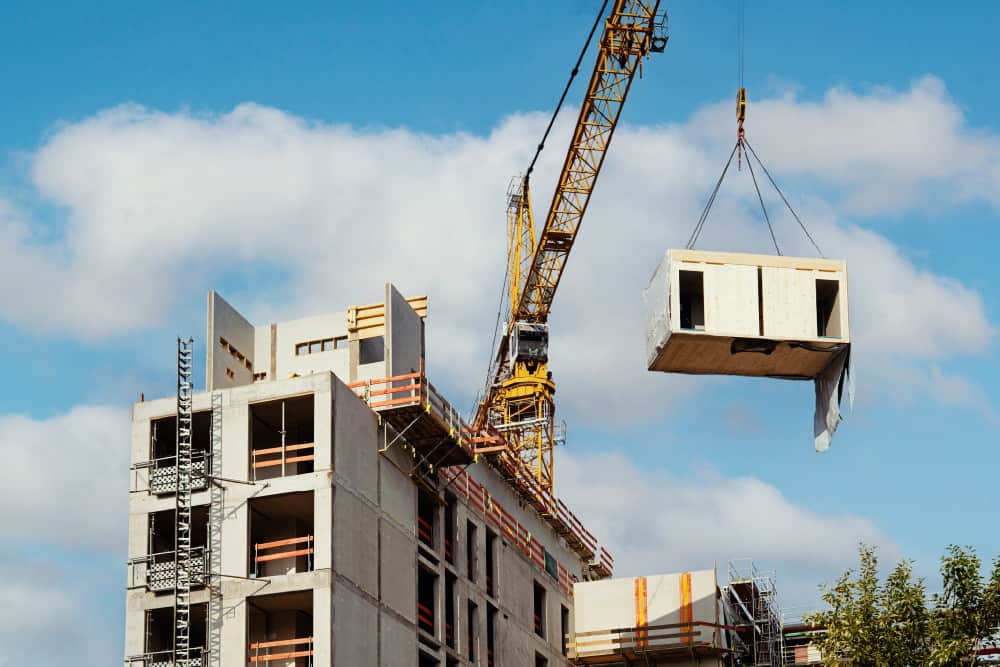
Lifting operations are performed daily in a wide range of workplaces, from healthcare facilities to warehouses and construction sites. When carried out incorrectly, lifting operations can cause serious injuries and can even result in fatalities.
LOLER is legislation covering all lifting operations conducted for work purposes. It places responsibilities and duties on anyone who owns, operates or has control over lifting equipment. The purpose of LOLER is to ensure that all equipment used in lifting operations in the workplace is safe for use.
In the following sections, we will provide a definition of LOLER, explain its principles, what equipment it covers and what duties it places on workers and employers.
What Does LOLER Stand For?
LOLER is the acronym commonly used for the Lifting Operations and Lifting Equipment Regulations 1998, enforced and overseen by the Health and Safety Executive (HSE). The HSE developed LOLER for the Health and Safety Commission in order to further strengthen the 1992 Manual Handling Regulations. It was made law under the Health and Safety at Work Act 1974 and expands on the obligations stipulated by the Provision and Use of Work Equipment Regulations 1998.
What is LOLER?
LOLER was created to ensure that all lifting operations conducted in the workplace that use lifting equipment are safe. LOLER requires that lifting operations be planned, supervised and carried out by competent individuals who are fully capable of working safely.
LOLER also sets out requirements for lifting equipment. It must be:
- Strong and stable enough to be used as intended.
- Marked to display its maximum load capacity.
- Regularly inspected and maintained to ensure it remains in good condition, with any defects recorded and reported.
- Stored correctly to ensure its longevity.
What Are the 3 Principle Aims of LOLER?
The three main aims as set out by the HSE are:
- Lifting operations must be properly planned and managed.
- Lifting equipment must be used in a safe manner.
- Lifting equipment must be thoroughly inspected at suitable intervals by a competent person.
What Is a Lifting Operation Under LOLER?
Regulation 8(2) of LOLER states that a lifting operation is “an operation concerned with the lifting or lowering of a load”. A load is defined as any item or object that is being lifted, including people and animals. Any time you are using a piece of equipment or machinery to lift something at work, these regulations apply.
What Equipment is Covered By LOLER?
LOLER regulations apply to a wide range of lifting equipment used in various types of workplaces, such as:
- Construction sites
- Factories
- Warehouses
- Hospitals
- Hotels and restaurants
- Offices
- Care homes
- Residential properties – if lifting equipment is used by homeworkers
Examples of lifting equipment covered by the LOLER regulations include:
- Cranes
- Lift trucks
- Telescopic handlers or booms
- Pallet trucks able to lift forks above 3 metres
- Rope and pulley systems
- Goods or passenger lifts in workplaces, such as those in an office block or a hospital
- Patient hoists
- Vehicle inspection hoists
- Mobile elevated work platforms (MEWPs)
- Rope systems used during tree trimming or working on telecommunication towers
- Vehicle tail lifts
Equipment NOT Covered By LOLER
It should be noted that there are certain types of equipment that LOLER does not apply to, such as:
- Conveyor belts
- Fall arrest ropes
- Escalators
- Equipment that may move up and down but is not designed to lift as a primary function, such as a plough
- Equipment that is only used by the public and not for work purposes, such as an elevator in a residential block of flats
- LOLER does not apply to ships unless land-based workers are put at risk
What are Employer and Employee Responsibilities Under LOLER?
LOLER makes a clear distinction between what employers and employees must do to ensure safe lifting operations.
Employer Responsibilities
Employers have a duty to ensure lifting equipment is not only suitable, marked and installed safely, but also maintained, managed and used in a way that reduces risks.
Beyond selecting the right equipment, employers must:
- Appoint competent persons to carry out thorough examinations and oversee lifting operations.
- Establish a clear inspection schedule, ensuring formal checks are carried out at required intervals and recorded appropriately.
- Provide written instructions and ensure they are understood by those expected to use the equipment.
- Monitor how equipment is used in practice, and take action where risks arise from misuse or poor condition.
- Ensure coordination between teams where lifting equipment is shared or used across different parts of a site.
These responsibilities go beyond compliance. They help reduce the risk of injury, equipment failure and enforcement action.
Employee Responsibilities
Employees who use lifting equipment have their own responsibilities under LOLER and the Health and Safety at Work Act 1974.
They are expected to:
- Use equipment as trained and in line with the instructions provided.
- Perform basic pre-use checks on equipment before work begins.
- Report faults or concerns immediately to a supervisor or responsible person.
- Follow site procedures related to lifting operations, including safe positioning and load securing.
- Cooperate with inspections and supervision, and never override or ignore safety features.
Employees also have a duty to take reasonable care of their own health and safety and that of others who may be affected by how they use lifting equipment.
Together, these responsibilities support safer lifting operations and help ensure compliance with UK law.
The Consequences of Not Complying with LOLER
Balfour Beatty was fined £285,000 in September 2024 after a worker died and another was seriously injured during a lifting operation at the University of Birmingham.
The incident occurred in January 2020, when two contractors were working from a scissor lift to install internal cladding. A nearby crane, operated by another team, was being used to move hydraulic equipment into position. The crane struck the scissor lift, causing both men to fall around ten metres. One worker died at the scene. The second sustained multiple serious injuries, including damage to his spine and pelvis.
An investigation by the HSE found that Balfour Beatty had failed to plan and coordinate lifting operations properly. There was no lift supervisor present and no effective communication between the separate teams working in the area. The company pleaded guilty to breaching Regulation 8(1) of LOLER.
The case highlights the importance of:
- Appointing a competent lift supervisor for all lifting operations
- Coordinating activities between contractors on-site
- Ensuring that lifting plans are clearly communicated and followed
Proper planning, supervision and control are required under LOLER. In this case, the absence of those basic safeguards had fatal consequences.
How to Provide LOLER Training to Your Staff
LOLER training is crucial if staff and management are to perform lifting operations safely. Completing accredited LOLER training that is provided by a professional, reputable provider will ensure that all risks involved in lifting operations are mitigated or eliminated.
If you are interested in LOLER training, the Human Focus LOLER training courses provide participants with a throughout knowledge of their responsibilities under LOLER and teach trainees how to perform risk assessments and lifting equipment inspections. These courses will make sure that your workplace stays safe and complies with legal obligations.