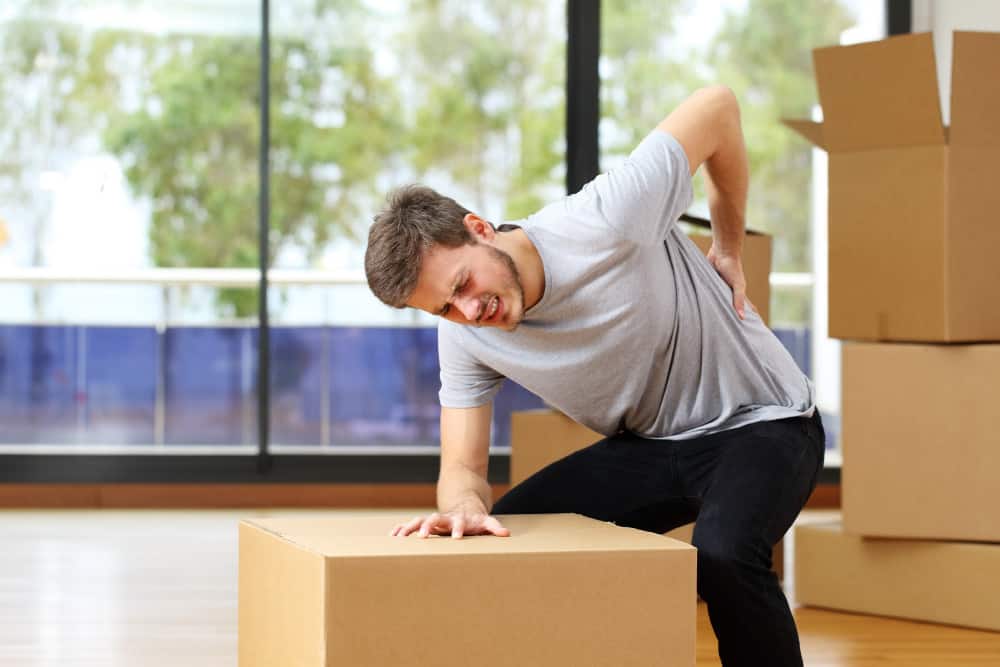
If you have studied manual handling techniques, you may have come across the term ‘TILE’. But What is TILE Manual Handling? TILE is a manual handling acronym that designates the process used to evaluate a task.
Understanding the TILE process is a good way of learning how to conduct an effective and efficient risk assessment on any heavy or light manual handling task. In this blog, we will look at the exact meaning of TILE in manual handling and how it can be used to make your workplace safer.
Why TILE is Important in Manual Handling
The large majority of manual handling accidents involve muscular sprains or strains, most commonly to the lower back. Less common, but no less serious, injuries involve cuts and fractures. These are typically a result of being crushed or hit by loads or equipment involved in manual handling tasks.
Due to the risk of injuries, all employers have a legal duty to risk-assess any foreseeable manual handling hazards. This risk assessment must be adequate, given the nature of the work. It should involve your staff as those at the sharp end know best where any problems are.
To help people assess the risk factors associated with manual handling tasks, the TILE Manual Handling process was devised by the Health and Safety Executive (HSE).
What Are the 4 Key Areas of Manual Handling?
There are 4 key areas abbreviated as TILE in Manual Handling:
- T – The Task
- I – The Individual/s carrying out the work
- L – The Load being handled
- E – The design of the workplace and the workplace Environment
Let’s look closer at these key areas of TILE in manual handling.
T – The Task
When performing a risk assessment according to the TILE manual handling process, the first aspect to consider is the nature of the manual handling task itself.
For example, in a warehouse operation, manual handling tasks might include:
- Unloading vehicles
- Moving stock into the warehouse
- Picking merchandise for customer orders and
- Loading vehicles with outbound orders
Alternatively, in an office environment, the list of manual handling tasks might involve:
- Moving stationery supplies
- Transporting files
- Removing rubbish
- Moving equipment or furniture
Assessing the task involves looking out for awkward postures that increase the strain on those lifting and handling.
The first posture to look for is bending at the waist. Your back is at its safest in an upright position with three natural curves present. But this changes dramatically by simply leaning forward. The back muscles contract in order to counter the weight of the upper body.
Your colleagues may not be in these leaning postures for long, but if repeated regularly, over time, they can lead to problems. The more the person bends over, the greater the load on the back. By bending their knees and keeping a more upright posture, the strain on the back is reduced. The greater the horizontal distance of the load from the body the higher the forces on the lower back. Keeping a load close to the body significantly reduces the strain on the back.
Twisting at the waist also increases the stress on your back. The position of the centre of gravity of the load can increase the strain. Moving your feet and keeping the load in front of you helps to reduce the forces and keep the centre of gravity as close as possible to reduce strain.
Lifting too much at once can exceed an individual’s capability. Splitting loads can help to keep forces within safe limits. If lifting is combined with bending and twisting at the waist, then even a relatively light load can cause significant stress to the lower back.
Pushing and pulling mechanical aids is another source of stress for the back, particularly if they’re fully loaded.
I – The Individual
A risk assessment must also take into account the individual or people carrying out the work. Even in a well-organised workplace with a convenient load, problems can arise if employees adopt poor handling techniques. There is a lot that individual workers can do to reduce the strain by adopting good lifting and handling techniques. Employees should be well-trained in correct manual handling techniques
Psychosocial elements should also be considered when assessing individuals. These can include:
- Tight deadlines
- The pace of the work
- Lack of control over work practices
L – The Load
The load itself can make the job difficult and should be thoroughly assessed. Loads might be very heavy, large or bulky. The weight may not be evenly distributed. There might not be anywhere to get a good grip. Does the size of the load make it difficult for an employee to see where they are going? Are there sharp edges or abrasive surfaces which can cause cuts or skin problems?
Is there a risk of dropping the load or crushing hands or feet? Could the load fall onto people passing by, or the person doing the handling? What would happen if either of these scenarios occurred?
If mechanical aids or vehicles are to be used, is it possible that they could be overloaded? Are they suitable for the job, in good working condition and regularly maintained?
E – The Environment
The last step in the TILE manual handling process is to assess the environment or workplace.
In your workplace, you should look out for features that may make it difficult for people to lift or handle loads safely. Workplace obstructions, perhaps caused by untidy areas, can force people to lift in the type of awkward postures that increase the risk of injury or accidents.
Examples include:
- Having to lean over and lift at arm’s length
- Twisting at the waist and
- Lifting either above shoulder or below knee height
You should pay particular attention to jobs forcing people to work in these types of awkward postures for long periods of the day or as a matter of routine.
Flooring is another important environmental aspect to consider. Are all areas kept tidy and free of tripping and slipping hazards? Do you have surfaces that are worn or misaligned? Do loads have to be handled up or down ramps, inclines, steps, or stairs?
You should also look out for areas where there might be poor lighting, which may increase the chances of an accident occurring.
Using TILE in Manual Handling Assessment
When moving loads, workers should be instructed to assess the work before beginning using TILE. Here are some other important tips they should follow:
- Don’t lift unless you have to, for example, use a mechanical aid instead
- When lifting, place your feet close to the load
- Bend your knees and not your back
- Get a good grip and keep the load close
- Push or pull objects to get them closer before lifting
- Avoid twisting at the waist whilst lifting
- Move your feet and try to be as mobile as possible
- When using mechanical aids, make sure individual items are secure
Never move very heavy or bulky items unless you’ve been authorised. If you must, plan the lift and make sure you have help. Try to separate individual items of a load that you consider heavy in order to reduce the burden.
Variations of TILE in Manual Handling: LITE and TILEO
LITE and TILEO are similar acronyms often used alternatively to TILE in manual handling risk assessment.
LITE stands for:
- L – The Load being handled
- I – The Individual/s carrying out the work
- T – The Task
- E – The design of the workplace and the workplace Environment
Whereas TILEO stands for:
- T – The Task
- I – The Individual/s carrying out the work
- L – The Load being handled
- E – The design of the workplace and the workplace Environment
- O – Any Other Factors that may not fall into the standard four categories, such as:
- The use of mechanical aids (e.g., forklifts, pallet trucks, or lifting equipment).
- The impact of fatigue and stress on manual handling performance.
- The presence of hazardous substances that could affect grip or increase risk.
Learn More about Occupational Manual Handling Safety
The TILE manual handling process can be used to develop efficient and effective risk assessments. If you would like to have your employees undergo safe manual handling training, then an online course can provide them with crucial information.
Human Focus offers the Manual Handling Training course, which provides trainees with a good grounding in manual handling techniques and principles. This training is approved by the International Institute of Risk & Safety Management (IIRSM).