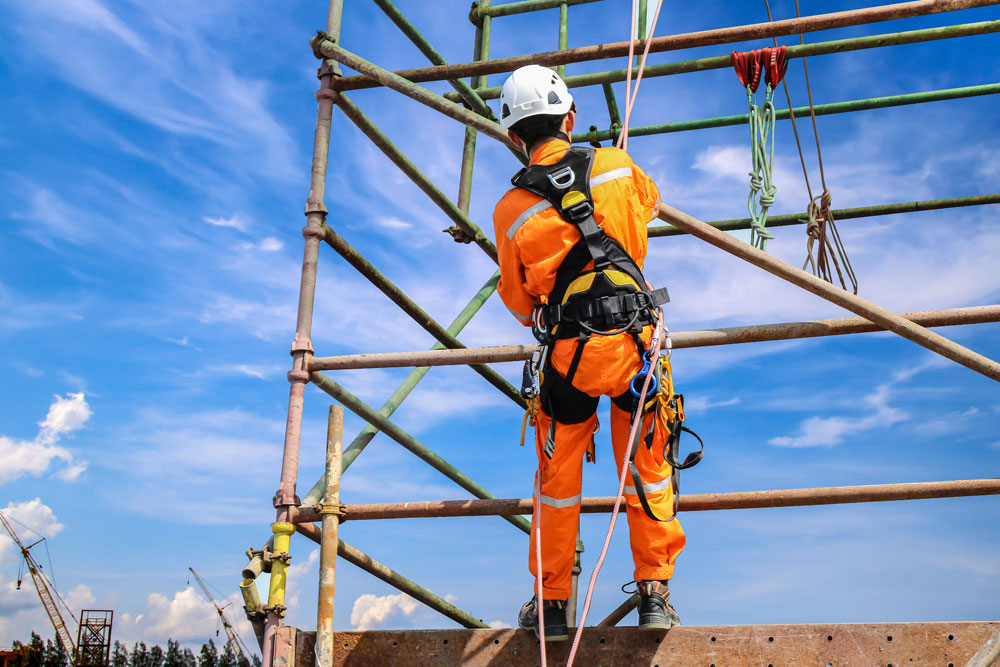
A safety harness can be the difference between life and death when working at height. But like any equipment, safety harnesses wear out over time. Eventually, life-saving fall protection equipment becomes nothing more than a high-visibility accessory. So when should a safety harness be replaced? This is a crucial question for anyone who works at height.
In this blog, you’ll find clear, practical advice on recognising when to replace your safety harness. This information will help you protect your workers, avoid accidents and comply with regulations.
Recognising When Should a Safety Harness be Replaced
When should a safety harness be replaced? Checking the manufacturer’s guidance is the first step in answering this question.
However, this guidance cannot account for the unique work conditions your safety harnesses will face, so it’s a loose guide at best. Instead, it’s safer (and necessary) to plan an inspection regime for your equipment to identify subpar equipment before it can be used.
Regular inspections are the key to ensuring the effectiveness of safety harnesses. They help you identify when a harness can no longer be trusted to protect your workers.
Why Regular Inspections Matter
Safety harnesses are vital for protecting workers from falls. However, harnesses wear out over time due to regular use and exposure to harsh conditions. A compromised harness can fail at a critical moment, leading to severe injuries or worse. Inspections help you spot these issues before they cause harm.
Types of Inspections
There are two main types of inspections that determine when to replace safety harnesses:
- Detailed Regular Inspections: These are thorough examinations carried out by a competent person. They identify subtle or hidden issues that might be missed during a quick check. If a harness fails any part of this inspection, it needs to be replaced immediately. Examples of failures include frayed webbing, damaged stitching or deformed hardware.
- Pre-Use Checks: These are quick visual examinations performed by the worker. Each worker should be trained to perform these checks every time they use their harness. It’s the last chance to catch and retire unsafe equipment before it’s used. If any obvious defects are spotted, like visible wear or broken components, the harness must be replaced.
Regular inspections and pre-use checks ensure that any issues are identified and addressed before they can cause harm. This proactive approach helps you maintain a safe working environment and know exactly when to replace a safety harness.
Duties of Employers and Supervisors
Employers and supervisors have a legal and moral responsibility to ensure the safety of their workers. Part of this responsibility includes maintaining and inspecting safety harnesses to guarantee they are in good working condition.
Legal Responsibilities
Employers must ensure that safety harnesses are inspected regularly and replaced when necessary. This includes:
- Establishing a Routine Inspection Regime: Implement a schedule that includes regular inspections by a competent person and pre-use checks by the users. You should design a schedule based on guidance from the harnesses’ manufacturer and your risk assessment.
- Documenting and Recording Inspection Outcomes: Keep detailed records of all inspections and any actions taken.
- Training and Competence: Ensure that inspections are carried out by competent individuals. Competence means the inspector should have the proper knowledge, training and experience to conduct a detailed and compliant inspection. Employees must also be trained on how to conduct pre-use checks and recognise when a harness is unsafe.
Establishing an Effective Inspection Routine
Creating a thorough inspection routine is essential to maintaining the safety of your workers. Here’s how to do it:
Follow the Manufacturer’s Guidance
Always adhere to the specific inspection and replacement guidelines provided by the manufacturer. These guidelines are based on extensive testing and are tailored to each harness’s design and materials. The manufacturer knows the materials and construction methods used in their products best and can provide the most accurate timeline for inspections and replacements.
Understand Minimum Inspection Requirements
The British Standards and the Health and Safety Executive (HSE) in the UK provide basic guidelines to ensure equipment remains safe and functional.
- Annual Inspections: British Standard EN 365:2004 recommends that a typical safety harness should be inspected at least once every 12 months.
- Six-Month Inspections for Webbing/Rope: HSE guidance document INDG 367 recommends that harnesses and lanyards made from webbing or rope should be inspected every six months. This is increased to three months for harnesses used in harsh conditions, such as in scaffolding or demolition work.
These minimum recommendations provide a basic level of safety and compliance but should be considered the bare minimum. Depending on your working conditions, you might need to inspect more frequently.
Use Your Risk Assessment
Adjust the frequency of inspections based on specific risks identified in your work environment and recorded in your risk assessment. Factors that may compel more frequent inspections include:
- Exposure to Chemicals: Harsh chemicals can weaken the materials of the harness, making it less effective.
- Extreme Weather: Regular exposure to extreme heat, cold or moisture can cause wear and tear.
- UV Exposure: Constant exposure to sunlight can degrade the materials over time.
- Heavy Use: If the harness is used daily or for extended periods, it will wear out faster.
By documenting these risks in your risk assessment, you can create a tailored inspection schedule that addresses the specific challenges faced in your work environment.
Post-Incident Inspections
Inspect any harness immediately after an incident where it was used to prevent a fall. Even if there are no visible signs of damage, the harness should be thoroughly checked or replaced to ensure it can still perform effectively.
Recognising When Immediate Replacement is Necessary
It’s essential to know when a safety harness must be replaced immediately. Regular inspections and pre-use checks will help identify these situations, but there are also specific circumstances where a harness should be retired on the spot.
- Failed Inspections: If a harness fails any part of a detailed inspection or pre-use check, it must be replaced immediately. This includes issues like frayed webbing, damaged stitching or deformed hardware.
- Missing Serial Number: Without a serial number, you cannot track the harness’s inspection history or verify its age. This lack of information makes it unsafe to use.
- Unknown Manufacturing Date: If you cannot determine the harness’s manufacturing or purchasing date, you can’t be sure it is still within its recommended lifespan.
- Unknown Last Inspection Date: If the last inspection date is unknown, the harness should not be used until it has been inspected by a competent person.
Trust Your Instincts
If you have any doubts about the safety of a harness, don’t use it. Even if you can’t identify a specific problem, it’s better to be cautious. Safety should always be the top priority.
Key Takeaways
Regular inspections and pre-use checks are essential for identifying when a harness needs to be replaced. Here are the key points to remember:
- Follow Manufacturer’s Guidance: Start with the manufacturer’s recommendations, but remember that the conditions in which your harnesses are used will affect their lifespan.
- Establish an Inspection Routine: Implement a robust inspection routine based on manufacturer and industry guidance and your specific risk assessment.
- Recognise When Immediate Replacement is Necessary: Be vigilant for signs of wear and tear, failed inspections, missing information and post-incident damage.
- Train Your Team: Invest in proper training to ensure that all inspections are carried out by competent individuals and that every worker knows how to perform pre-use checks.
Harness and Lanyard Inspection Training
Ensuring that your safety harnesses are regularly inspected and replaced when necessary is a critical aspect of workplace safety. To help you achieve this, we offer IIRSM-approved Harness and Lanyard Inspection Training that walks duty holders through the process of deciding on an inspection regime as well as actual inspection procedures for common forms of fall arrest equipment.
- Learn Inspection Procedures: Gain in-depth knowledge on how to conduct thorough inspections, identify potential issues and understand when to replace harnesses and fall arrest and restraint lanyards.
- Prove Competency: Completing the course and earning certification is crucial for developing and proving the competency needed to inspect fall arrest and restraint equipment in line with regulations.
Don’t wait until an incident occurs. Enrol in Harness and Lanyard Inspection Training today and develop the knowledge to answer the crucial question: When should a safety harness be replaced?